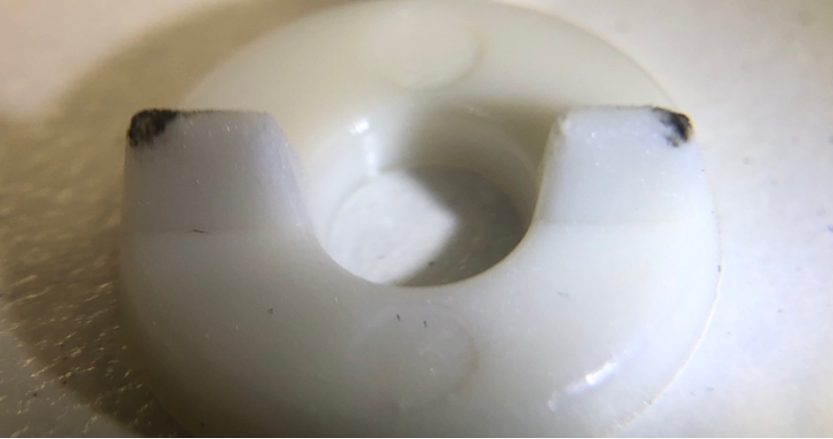
この記事では、射出成形における主な成形不良の種類と原因について詳しくご紹介します。
射出成形の成形不良とは
射出成型とは、加熱して溶かした材料を金型内に注入し、冷却、固化して製品を成形する加工方法です。プラスチックなどの樹脂を使用した射出成型の代表的な課題には「成形不良」があります。
成形不良とは、射出成型の製造工程において製品の外観や性能に不具合が発生することです。その原因はさまざまあり、製品に生じる不良の種類もいくつかあります。
成型不良は、廃棄しなければならない製品を増やすだけでなく、原因調査や対策に多くの人員・材料・時間を要します。そのため、射出成型の製造工程では、成形不良の原因となる要素を適切にコントロールする必要があります。
ヤケ(ガス焼け)
ヤケとは、金型内の樹脂が高温になり、成型品の表面に変色が表れる現象のことです。ヤケの主な原因は、金型内のガスの滞留や圧縮です。 金型に樹脂の流れが悪い箇所があり、金型内の空気や材料から発生したガスが滞留すると、樹脂が発熱し、高温になります。
ヤケを防ぐ主な対策は、空気やガスを排出するガス抜き部品の設置です。射出速度や圧力を下げる、成形温度を下げる、滞留時間を見直すなどの改善も有効です。
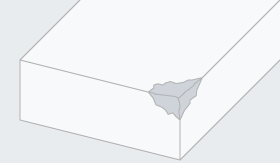
シルバーストリーク(銀条)
シルバーストリーク(銀条)とは、成型品の表面に銀白色の筋状の模様が発生する現象です。主な原因は、樹脂のなかで発生したガスが金型内で樹脂とともに引き延ばされるように流れることで、成型品の表面にガスによる流動痕が生じます。
シルバーストリーク(銀条)の原因は他にもありますが、ガス抜き不良が原因の場合は、金型内にガス抜き部品を設置することが有効です。金型以外の成形条件では、樹脂の乾燥不足や材料温度、射出速度・圧力の調整などが対策となる場合もあります。
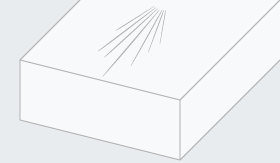
ウェルドライン(樹脂合流線)
ウェルドラインとは、金型内で樹脂が合流する部分で成型品の表面に筋状の不良が生じる現象です。外観が損なわれるため意匠部品では不良品となるほか、損傷の原因にもなります。
ウェルドラインが生じる主な原因は、金型内で分岐した樹脂が再び合流する際の融合不良です。融合不良の原因は、金型内のガス、金型設計による樹脂の流動性不良、射出温度・圧力などさまざまなケースが考えられます。 金型内のガスの滞留が原因と考えられる場合はガス抜き部品の設置が有効です。
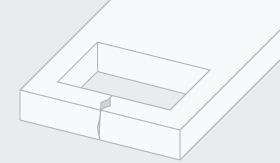
ショートショット(充填不足)
ショートショット(充填不足)は、金型の一部に樹脂が充填されない状態で成形される不良のことです。
ショートショット(充填不足)の原因は、樹脂の不足や流動性の悪さなど材料に起因するもの、金型の温度が低い、射出の圧力不足など成形時の条件に起因するものなどがあります。
ショートショット(充填不足)を防ぐ対策には、注入する樹脂の量の見直し、材料の流動性の見直しなどのほか、射出圧力を高めるなど成形条件を調整することが考えられます。
また、金型内に空気だまりができることでショートショット(充填不足)が生じている場合は、金型のガス抜き対策が必要になります。
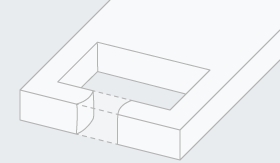
ソリ(反り)
ソリとは、射出成形された成形品の一部が反る現象のことです。特に、板状や箱状の成形品ではよく見られる不良です。ソリはさまざまな要因によって引き起こされますが、金型の温度差による樹脂の収縮や成形条件、製品形状(急激な肉厚の変化)などが考えられます。
ソリを防ぐ対策は原因によってさまざまですが、金型の温度を下げる、射出圧力や樹脂温度を調整する、肉厚を均一化するなどの方法が考えられます。金型の温度差が原因と考えられる場合は、3D冷却回路の設置が有効です。
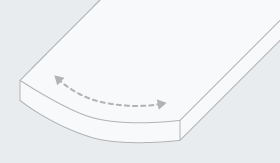
バリ
バリとは、射出成形をする際、金型からはみ出した材料によって成形品に不要な突起などが生じる不良のことです。バリが生じる原因はさまざまですが、金型の精度が低い、金型の締め付けがゆるい、樹脂などの材料温度が高い、射出速度が速い、パーティングラインにある圧縮されたガスが樹脂とともにパーティングラインからはめ出る現象(ガスバリ)などが考えられます。
バリを防ぐ対策も原因によってさまざまですが、金型に起因する場合は入子や溶接で修正し、隙間をなくします。また成形が要因の場合は、型締め圧を高める、樹脂温度を適正にし、ゲート調整を行うなどの対策を行います。ガスバリが要因である場合は、金型のガス抜き対策が有効になります。
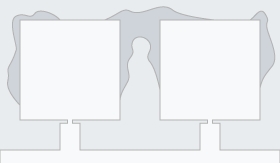
クラック
クラックとは、金型から取り出した成形品の表面にヒビが発生する、成形品が割れるなどの現象が生じる不良です。 主な原因は、金型の内部に生じる内部応力と、金型を外す際の圧力です。前者は、樹脂の硬化速度が不均一な場合に起こります。後者は成形品を型から外す際に歪みが生じ、成形品に余計な圧力がかかることでクラックが生じます。また、箱形状の場合は取り出し時に金型と製品空間が真空状態となり、取り出しに過剰な圧力がかかることでクラックが生じる場合もあります。
硬化速度が不均一な場合は、金型温度を上げ、冷却時間を長くするなどの調整を行います。型から外す際に歪みが生じる際は、抜きテーパーを多めに取る、突き出しピンを追加するなどの対策が有効です。また、真空状態を解除するために、ガス抜き対策が有効になります。
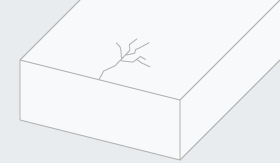
ジェッティング
ジェッティングとは、成形品の表面にヘビが這ったような蛇行した跡が生じる不良のことです。先に射出された樹脂が金型面で温度が低下したことで固化し、 後から入ってきた溶解した樹脂に流され跡を残すことが原因であると考えられています。
射出速度が速い場合に起きやすい現象のため射出速度を下げるほか、先に入った樹脂が固まらないように金型温度を上げる対策が効果的です。
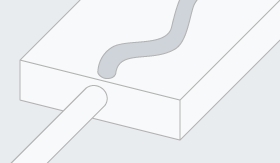
フローマーク
フローマークとは、成形品の表面に樹脂が流れた跡が残る不良の総称です。溶融した樹脂が金型内を流動する途中で冷えると、固化し始める部分ができます。 後から来る樹脂の流れで固化しかけた部分が押し出され、波状の模様が生じます。このような状態が生じる主な原因は射出速度にあります。
樹脂の固化は射出速度が遅いほど進みやすくなります。そのため、射出速度を速くすることがフローマークの対策となります。
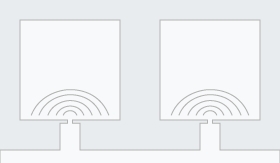
ボイド(気泡)
ボイドとは、成形品の内部に気泡が生じる不良のことです。特に、樹脂を厚みのある形状に成形する際に起こります。肉厚部分の表面が先に固まると樹脂は収縮し、表面に引き寄せられます。 そのため、遅れて冷却される内部に気泡が生じた状態で固まります。
このように、ボイドの原因は肉厚成形品の表面と内部の冷却温度差による樹脂の収縮であるといえます。対策としては、射出成形条件の調整や、金型のガス抜き対策、肉厚を薄くするなど成形品自体の形状の改善なども考えられます。
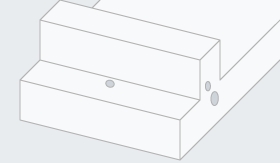
ヒケ
ヒケとは、成形品の表面に歪みやへこみが生じることです。樹脂は熱すると膨張し、冷やすと収縮します。ヒケは、樹脂が冷える際に異常な収縮が起き、発生する現象です。とくに成形品の肉厚差が大きい場合に生じやすくなります。
対策としては、設計段階から成形品の肉厚を調整することが有効です。また成形条件による対策では、保圧時間を長くする、成形温度を上げるなどの方法が考えられます。また、金型の対策では、金型温度を上げることで解決する場合もあります。
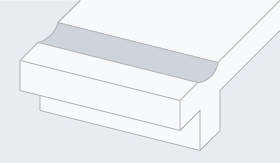
まとめ
このように射出成形時の成形不良は、さまざまな要因で起こります。その解決策も、原因によって金型の対策、成形条件の調整、材料の改善、成形品形状の見直しなどさまざまです。記事内ですべてをご紹介することはできませんが、主な原因と対策を把握することで成形不良の要因を推測しやすくしましょう。
金型内のガスを要因とする成形不良の解決方法
当社のガス抜き部品は、微細貫通多孔質素材であるため「樹脂が流れ込みにくいが、気体は通す」通気孔として最適なバランスになっています。
ガスに起因する成形不良(ヤケ、白濁、銀条、ウェルドライン、ショートショット、ヒケ、バリ等)の改善に役立つほか、金型メンテナンス周期の延長や金型耐久ショットの向上にもつながります。
成形機ノズル部に滞留したガスが製品部分まで流れ込むことは、さまざまな成形不良の要因となります。製品部分へのガスの流れ込みを防止するさまざまな商品をラインナップしていますので、成形不良でお悩みのお客様はぜひお問合せください。
成形不良対策部品「GASEXIT」
微細貫通多孔質素材によるガス抜き部品で、成形不良をソリューションします。
樹脂が流れ込みにくく、気体は通す通気孔として最適なバランスになっています。
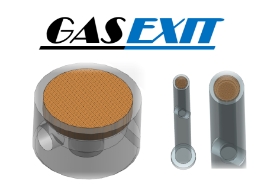